
Drive Failure
Industrial Drive Failure with power electronic-based AC VSD and DC Drive or computer hard disk drive, results in a power system with crammed harmonic energy sources. VSD and DC drives are NLL and harmonic generators. The solution is between costly derating or efficient harmonic solution as applied in this case study.
In an industrial environment, the workstation's computer hard disk drive or data centre server's hard disk drive gets power through UPS. But UPS passes on momentary input voltage surge as dc ripple to its output and thus can't protect its loads from input voltage fluctuation.
In-addition computer and servers loads at the UPS output generate zero-sequence harmonic which triples at neutral, causing high neutral current which tends to increase neutral voltage. Its effect fails the traditional protection devices like SPD and MOV. Encon facilitates the best solution in eliminating hard disk drive failure from voltage surge.
An ACSR conductor manufacturing plant was facing high incidence of DC motor and AC VFD Drive Failure due to bad power quality and high harmonic distortion. The company is a world leader in non-ferrous metal industry. It manufactures ACSR conductors for HV and EHV power transmission and distribution lines. It had been facing a high incidence of operational problem across its plants A and B. It affected all electrical and electronic equipment with its conductor making process. In-addition, there were daily process interruptions due to nuisance tripping of DC/ VFD Drives. The problem arose because of two reasons. First, it was using over 60% Non-Linear-Loads in the forms of DC-drives in rolling mills, Variable-Frequency-Drives (VFD) in the conductor making process and PLC in control system. Second, it was operating at high load factor, in between 80 to 100%, of its transformer capacity. Load Factor is the actual running-load in mW/mVA divided by upstream transformer or diesel generator capacity in mW/mVA. World-wide most factories, buildings, and facilities, with similar nonlinear load profiles, run safely at around or even below 40% load factor. This is to keep most power qualities and harmonic problems under the carpet within its latent stage. Root cause of these are the rise in Total Harmonic Distortions, both THDv (voltage), and THDi (current), whose magnitudes are directly proportional to the plant's operating load factor; and that explains why de-rating helps in skirting the problem albeit with a guzzling infrastructure. The company was at the top of competition chain among peers.
Fortunately, there exists an alternative that can effectively bring down harmonic distortions, both THDv and THDi, and improve the quality of power within an electrical power system. This is the domain and usefulness of Tuned Harmonic Filter that when designed appropriately reap rewards one can count on. It reconstructs the distorted waveform back into sine waves, thereby debottlenecks equipment capacity limitations, and removes barriers to energy efficiency from the plant and machineries; and transforms them instantly into impossible is nothing like performances, snippets of which are presented here.
We installed four sets variable tuned harmonic filters, 500A, 1000A, 2000A and 4000A for 750kva, 1500kva, 2000kva and 3150kva transformers respectively. Each transformer was backed up by an appropriate sized back up DG. Each harmonic filter was designed to cover full load of its transformer, and backup DG, and were installed at the 415v main incoming LV PCC of each transformer, and its back up DG. The harmonic filters were designed for operating either with the grid/transformer source or the backup DG source, and the changeover between the grid-to-DG and DG-to-grid as well as adjustment in the plant's load variations, were accomplished automatically within the harmonic filter panel logics.
Industry Background: Overview of power transmission industry: The Indian Ministry of Power has projected an addition in installed capacity of 68,869 MW during the Eleventh Five Year Plan (2007 to 2012). The goal in Eleventh Five Year Plan is to achieve a national power grid with inter-regional power transfer capacity of more than 37,000 MW. (Source: http://www.the-finapolis.com). The state-owned company, Power Grid Corporation of India Ltd, owns and operates a power transmission network, as on January 01, 2008, of 64,700-CKT-KM, 110 Sub-Stations, 66,650mva of Transformation Capacity and has established a national grid with an inter regional power transfer capacity of about 17,000 MW (Source: http://www.bseindia.com).
The factories under this case study follow international standards for quality, productivity, and safety. It is a leading global supplier of power transmission equipment. It also has a fully integrated optical fiber production facility and ranked among top 5 global manufacturers of transmission power conductors. Its manufacturing range covers from Extra High Voltages (400 kV - 800 kV), High Voltages (66 kV - 220 kV) to power distribution conductors (11 kV- 33 kV).
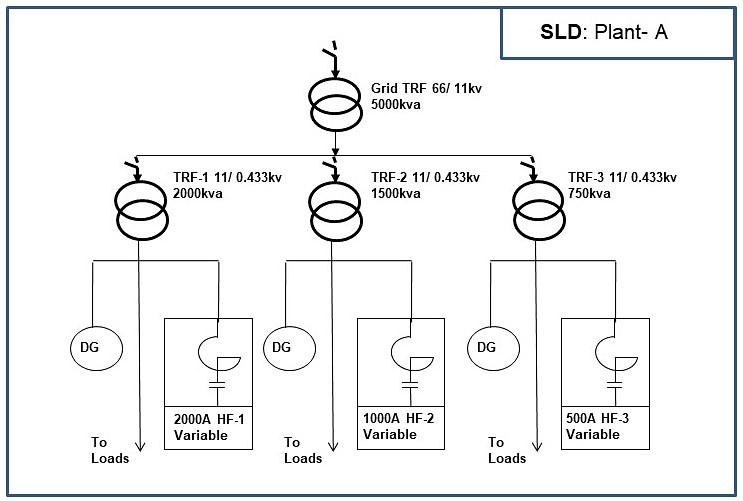
Problem Statements: These plants were encountering PQ and harmonic distortion problems in the forms of frequent nuisance tripping and equipment failures, often unseen, and unknown. It was also facing over temperature issues across most equipment, lower power factor and higher KVA demand. It availed exclusive 66kv transmission line from the utility company, for avoiding voltage fluctuations, but was still plagued by the conventional Power Quality issues, of equipment nuisance tripping on the momentary fluctuations/sags of grid voltage. However, after commissioning of harmonic filters all problems got resolved that including nuisance tripping because of momentary grid voltage fluctuations/sags.
At plant-A, the grid supply was drawn through a dedicated 5.0mva, 66kV/11kV upstream grid transformer, and followed up by 3nos downstream transformers, namely 750kva, 11/0.433kv (500A harmonic Filter installed at 415 Sec.), 1500kva, 11/0.433kv (1000A harmonic filter installed at 415v Sec.) and 2000kva, 11/0.433kv (2000A harmonic filter installed at 415v Sec.) for downstream loads. At plant-B, the grid supply was drawn directly by 2nos downstream transformers each 3150KVA, 11/0.433kv (2nos 4000A harmonic filters installed at 415v Sec. of each transformer) for downstream loads.
1. Nuisance Tripping: Happens with moderate rise in THDv typically above 5%. Since THDv is omnipresent throughout the power system, it affects all power electronic drives -VFD /DC, PLC and associated Control Systems everywhere those are connected within the same transformer supply. Distorted waveform has plethora of up and down spikes/fluctuations. Drive's control and protection system mistake them as fault condition, and initiate tripping action once it exceeds the threshold limit. For example, it could trip annunciating an over-voltage, over-current or earth condition, even though nothing like that seemed to have happened. Motors with digital controls are more prone to nuisance tripping than with analogue controls. Plant engineers do not find specific reason for such tripping and on reset, the drive runs as normal. In these plants nuisance tripping was happening, few times, every day basis, with every odd voltage fluctuations/sags from the grid or the internal power system. This is because THDv was hovering at a much higher level of, between 10 to 15%.
2. Electronic Failures: Happens when THDv rises considerably higher, typically above 7%. THDv being omnipresent affects all equipment those are connected within the same transformer supply. Electronic-VFD/ DC/ Drive Cards are the first to fail- burn/ flash/ blast, being more susceptible to harmonic distortions, followed by PF correction capacitors, fuse, motors-ac/dc/servo/eddy-current, ct, pt, switchgear, transformer, cable and terminations. Rising THDv stresses all equipment and reduces their life. At plant-A alone, one-electronic drive used to fail/burn on an average, every month.
3. Motor Failures- SQIM, SRIM and DC: Happens when THDv rises much higher, typically above 9%. THDv is omnipresent that affects all motor types within the same transformer supply. These failures are often mistaken as overload burning.
Plant-A, has squirrel cage induction motors (SQIM) between 5 to 30hp, both constant speed and with VFD drives. Initial harmonic problems show-up in the forms of higher bearing temperature and/or phase current imbalance. Slowly it leads to stator winding failure either burn or open-up. Monthly about 10% of all running SQIM used to fail.
Plant-A, has slip ring induction motor (SRIM) between 50 to 150hp. Initial harmonic problems show-up in the forms of high bearing temperature and/or phase current imbalance. Slowly it leads to stator winding failure either burn or open-up. In-addition, external rotor copper winding link, ring and/or the resistance (air-cooled) used to burn. On Occasions, typically once in a year even the sturdy rotor winding used to burn. Monthly about 3% of all running SRIM used to fail.
Plant-A, has DC Motor between 5 to 450hp. Initial harmonic problems show-up in the forms of field over current. Slowly it leads to field winding failure either burn or open-up. Commutator gets overheated. It leads to irregular gap between commutator segments as soldering bond between them give-up. Even with extreme care and monthly maintenance schedule, there used to be occasional commutator burning. Occasionally, and typically half-yearly, even the sturdy armature winding used to burn altogether in about 3 to 4 slots. Monthly about 5% of all running DC Motors used to fail/burn. Motors with analogue controls were found more prone to field winding failures and motors with digital controls to nuisance tripping.
4. Capacitor failures: In these plants, harmonic distortions (THDi about 50% and THDv about 15%) were so high that the capacitors used to blast frequently. Usually capacitors keep failing without giving out much signals, that keeps reducing its effective kVAr output. It necessitated frequent replacement of capacitors. In-addition, capacitors themselves contribute in magnifying harmonics, both THDi and THDv, to an extent that is determined by the short-circuit impedance of the power system, the connected capacitive impedance, and the extent of nonlinear loads in the power system. As a rule of thumb, more the capacitors installed, more would be the rise in harmonics, both THDv & THDi, which further complicates the power quality problem.
Low power factor systems are less efficient in utilisation of electrical power. Historically the simplest solution is to add capacitors for correcting inductive loads. However, such approach creates serious operational problems, if harmonics are present in the power system. Any combination of capacitance and inductance forms a circuit which get tuned to what is called towards a "RESONANCE FREQUENCY". It is the frequency at which both capacitive and inductive reactance of the power system equals. If significant harmonic energy is present in the power system, and its frequency matches with that of the resonant circuit formed by PF correcting capacitor and the system inductance, it would excite current into an oscillation. It results high harmonic currents, and that in turn further magnify the harmonic voltage. Its effect could damage equipment and reflect in excessively high harmonics in the entire power system. In addition, since the high oscillation current in the resonant circuit is wasted and no useful work is done, it drops PF further. However, capacitors do not themselves create any harmonic problem but their presence in the system with nonlinear loads aggravate a potential harmonic problem. Many a times harmonic related problems show-up after introduction of capacitors.
5. Switchgear- ACB/MCCB, Cable, termination and lug overheating & burning: Harmonica are like a current source, flow back from downstream wherein it gets generated to upstream, as it offers the least impedance path to its flow. Harmonics are high frequency currents (or voltages), for example, 5th harmonic is 250/300Hz current or voltage. On the other hand, the plant and machineries are designed for a 50/60Hz operation. Thus, all alone its flow path, harmonics cause excessive heating, energy losses, and premature ageing for cables, plant and machineries, equipment, switchgears, and transformers.
At plant-A, cables and terminations, which normally should operate at about 10oC above its ambient temperature, used to have even 20oC to 30oC above its ambient temperature, mostly at their termination points, wherein the lugs and cable insulations used burn. It used to happen on an average of once in every 3-months. That apart, good numbers of MCCBs and SFU units which were supplying to the capacitor feeders, used to blast frequently.
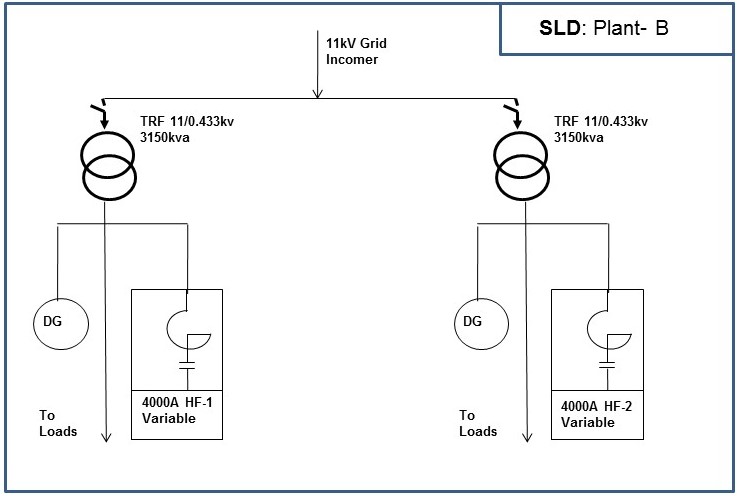
Objectives : In these plants, harmonic distortions were very high, THDi was around 50%, and THDv was around 15%, which resulted in bad Power Quality and high harmonic distortions in its electrical power system. With such high harmonics, nuisance tripping and equipment failures were almost like an everyday issue. Summarizing all benefits those accrued, with the post installation scenario of the harmonic filters, the objectives of a power quality improvement and harmonics distortion mitigation project shall be as follows.
1. To achieve the highest Profitability.
" The secret to highest profitability is simple, reduce cost and increase earnings. First, it could operate sustainably in the post harmonic filter implementation scenario, at an overall equipment load factor of over 80% up to 100%. Second, equipment tripping got eliminated. Third, with improvement in product quality, the quality check rejections got reduced by a whopping 50% at a Six Sigma scaling. Increased production considerably reduced CAPEX, the Project Investment Costs on deemed expansion, and with its associated financial holding costs. Increased energy efficiency and mitigation of tripping and failure issues considerably reduced OPEX, the plant's Running Costs, due to a reduction in monthly energy bills and maintenance costs. Achieving the highest possible product quality reaps premium sales realization value. Minimizing rejection and improving MTBF (mean time between failures), further enhance productions.
2. To achieve the highest Energy Efficiency and promote Green Energy.
" Bad Power Quality and harmonic distortions are less efficient in utilizing electrical energy that depending upon the complexity of the harmonics distortions. In-addition, equipment de-rating causes further energy losses. Topping it further, a lesser productivity creates further energy losses. We followed up the data for 6-months before the harmonic filter scenario and 6-months after filter installations, and it was certified to have achieved 9% kWh energy savings, and 20% kVAh demand savings.
3. To Troubleshoot operational issues those are attributable to none among the conventional causes of failures, and hence fall under the category of Power Quality and/or Harmonic Failures.
" These plants had an history of considerable equipment failures and nuisance tripping with its continuous process equipment, because of voltage fluctuations/sags from the grid and internal power sources. After the harmonic filters were installed, all tripping issues and failure problems got eliminated. Furthermore, it considerably enhanced life of its plants and machineries, since harmonic distortions cause premature aging.
4. To achieve highest possible Productivity.
" We had closely monitored its production data 6-months before the installation of harmonic filters and 6-months after its installations. It was certified that overall production increased by 25%, mainly because of two reasons. First, as equipment tripping and failures were eliminated, the plant's mean Time between Failures the MTBF rate, improved dramatically allowing uninterrupted production. Second, the stage wise quality check product rejections, got eliminated by 50% on a Six Sigma scale, which directly got transferred from the waste to become useful and quality end products.
" These plants were manufacturing multi-strand ACSR Aluminium conductors, typically 8-strands to 48-strands, and up to predefined length of between 1.80 to 2.10 kM. First, somewhere in the middle, few strands used to shear-out. And the way out was to solder them. But it always raises product quality issues apart from lowering production capacity for halting in-between and idling man-power. Post harmonic filter solutions, it almost got eliminated. Second, another problem, was with the rejection of entire length at the manufacturing end, on higher lay-ratio, which is slackness in-between strands of conductors that reduces the overall current carrying capacity of the conductor. Its major cause was nuisance tripping. On an average, there were about 1% of such rejection, before installing the harmonic filters, and it reduced to its logical minimum of less than 0.5% on the post harmonic filter solution scenario. On a Six Sigma scaling, it improved by 50%.
5. To achieve and maintain near UNITY PF, sustainably.
" Conductor and steel rope wire manufacturing process employ highly variable and mostly nonlinear loads of over 60% of its total load. PF correcting capacitors are not suitable to be used with such nonlinear loads. It used to fail- degrade/ flash/ burn/ blast rapidly. The plant management was facing tough time maintaining PF, and needed frequent replacement of capacitors but due to high harmonic distortions, PF did never improve at its desired level. After the harmonic filter solution, 6-months before and 6-months after data monitoring, it was certified that PF was steadily maintained near UNITY, and reflected at the utility's monthly energy bills, after the harmonic filter installations.
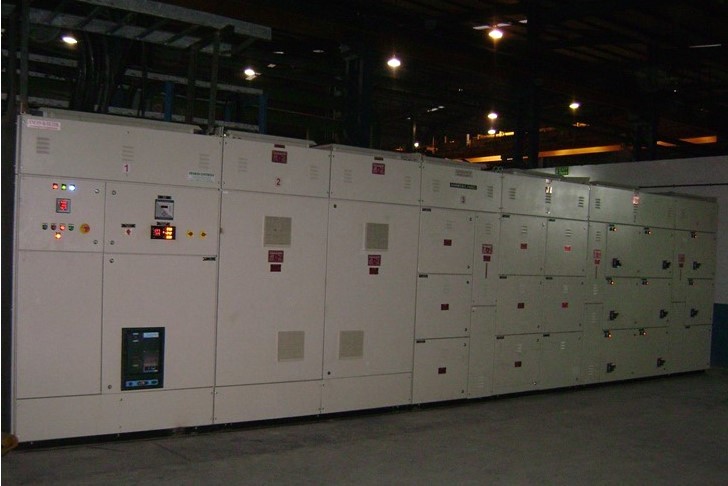
The Power distribution- SLD vis-à-vis the Solution provided: At Plant-A, the Grid supply was drawn through a dedicated 5.0mva, 66kV/11kV grid transformer followed by 3nos downstream transformers of 750KVA (500A Filter used), 1500KVA (1000A Filter used) and 2000KVA, 11/0.433kv (2000A Filter used) for downstream loads. Each transformer had its back-up 433V DG supply. Three harmonic filters were supplied, across each transformer's main LV PCC bus bar, which was also the main incomer of its back up DG supply, as shown in Fig.1.
Fig.3: 4000A harmonic filter for a 3.15mva TRF.
At Plant-B, the Grid supply was drawn directly into 2nos downstream transformers each 3150KVA (4000A Filters used), 11kV/0.433kV for downstream loads. Each transformer had its back-up 433V DG supply. Two harmonic filters were supplied, across each transformer's main LV PCC bus bar, which was also the main incomer of its back up DG, as shown in Fig.2. Followings were the typical load details for each conductor line, and these plants had multiple process lines for a diverse product portfolio.
Nonlinear Loads > 60%
" Rolling Mill, HRM, 595kW, dc
" Rod Breaking Down, CRM, 662kW, dc
" Skip m/c, 104kW, dc
" Tubular m/c, 46kW, dc
" Rigid Stranding, RST, 165kW, dc
" VFD and other process loads
Linear Loads
" Other Induction loads, SQIM & SRIM
" Oil Furnace
" Auxiliaries
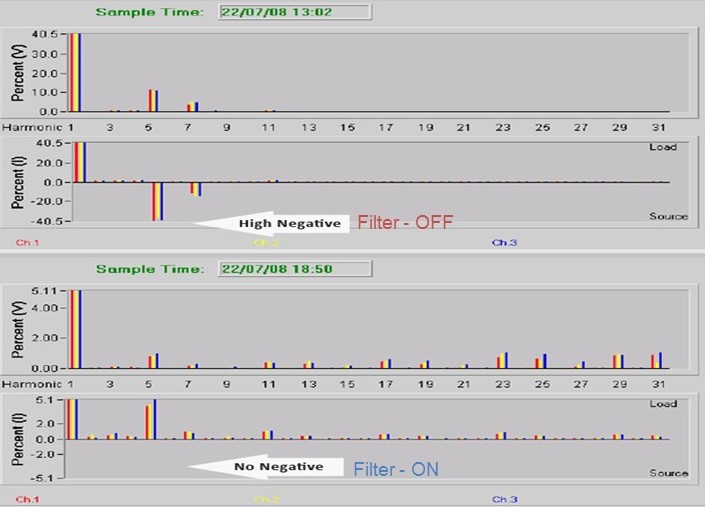
Technical Performance and deliverables of Tuned Harmonic Filters: The current and voltage harmonics and waveform distortions at the 415v transformer secondary PCC of 3.15mva transformer, before and after installation of 4000A tuned harmonic filter, are as shown in Fig.4 and Fig.5. Because of major nonlinear loads in the forms of DC and VFD Drives, harmonic distortions were very high, before harmonic filter installation. Total current harmonic distortions (THDi) were at 50% with I5, I7, and I11 as major current harmonics. Total voltage harmonic distortions (THDv) were at 15% with I5, I11, and I7 as major voltage harmonics. After harmonic filter installation, THDi reduced from 50% to 6%, and THDv reduced from 15% to 4%. Whenever a plant with major nonlinear loads employs harmonic filter and mitigates harmonic distortions, it's like driving the same car with the hand-break removed. To the similar extent, the electrical power system of the plant gets alleviated, due to the correction of its waveform distortions, both voltage and currents, as shown in Fig.5., before and after.
THDi acts like a current source. Gets generated by the nonlinear loads at downstream and flows back upstream as it offers least impedance path. All alone its flow path it causes excessive heating and failures in electronic drives, switchgears, capacitors, transformers, cables, and terminations. It injects energy losses, and causes premature aging. Unlike THDv, it can't easily pervade through the downstream equipment unless through a series resonance, which could occur at the interaction with its electrical power system. A series resonance condition could cause good damage in plants and machineries.
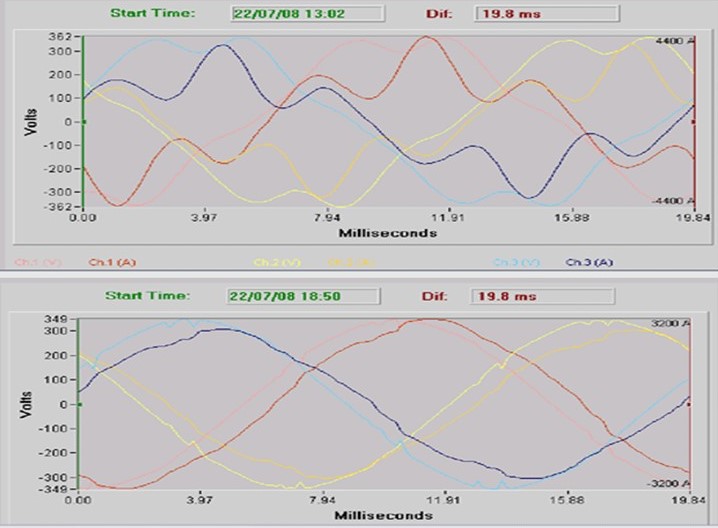
Reconstructing waveform distortions: Referring to Fig.5 recording for waveform distortions before harmonic filter installation, it is observed that the waveforms were highly distorted with series of limitless spikes and peaks both at the up and down directions. These high fluctuations, sags and swells of the incoming supply voltage and in currents (similar fluctuation happens with current waveform), which are actual running loads, are picked up by protective relays, and once it exceeds its threshold limit, initiate tripping actions. It explains why there were so many nuisance tripping in those plants, few times, every day, at every odd voltage fluctuations/ sags/ swells from the grid/internal supply. On the other hand, after its installation, the harmonic filters could reconstruct the distorted waveforms back into its original sinusoidal form. Thus, it could eliminate the fluctuations, sags and swells from the incoming supply voltage, and the same way, fluctuations from the plant running load currents. This explains the reason for the nuisance tripping to get eliminated, after harmonic solutions were provided. In-addition, pure sinusoidal waveforms are most efficient in the utilization of electrical energy than distorted waveforms, wherein good amount of energy is wasted away as heat, noise and vibrations in the plant equipment and power system's cables and bus bars. These vibrating torques further create lesser product quality.
Conclusion: The study clearly establishes all round improvement in major parameters that lead to better and improved quality of power in the plant's electrical power system. Benefits of having better power quality were clearly established in the specific terms of enhanced productivity, lesser running costs, and higher profitability. The cost savings when looked narrowly in comparison to electricity bill alone might seem moderate but when compared holistically with the savings with initial project investment cost, interrupted production cost, maintenance cost, inventory cost of components and maintaining workforce's motivation coupled with the ever-rising energy costs; the economic benefits of improving power quality far outweigh the cost of its solution.
BIOGRAPHIES
Kanai Banerjee graduated in Electrical Engineering from Indian Institute of Engineering Science and Technology, Shibpur, India in the year 1983. Worked at Bharat Heavy Electricals Limited from 1983 to 1995 and thereafter until date, as a promoter at Encon Engineers (www.enconengineers.in/) in Bangalore.
His special fields of interest include power quality engineering, harmonic solutions and manufacturing passive tuned harmonic filter and triplen harmonic filter of all size LV and HV, troubleshooting failures, energy conservation, electrical consultancy, and HVAC engineering for setting up truly green building and retrofitting large centralized HVAC projects.
He has been instrumental in building up the company's impressive growth and reputation as a knowledge-based technology solution provider on power quality, energy efficiency, process optimization and in Total Power Management fields.
An energy auditor certified by the bureau of energy efficiency under the ministry of power government of India, a member and chartered professional engineer with the institute of engineers, India, a member at the Indian society of heating, refrigerating and air-conditioning engineers, ISHRAE and a member at the Canadian and American EMTP-ATP user group.
Place: Bangalore
Date: 30th July 2008